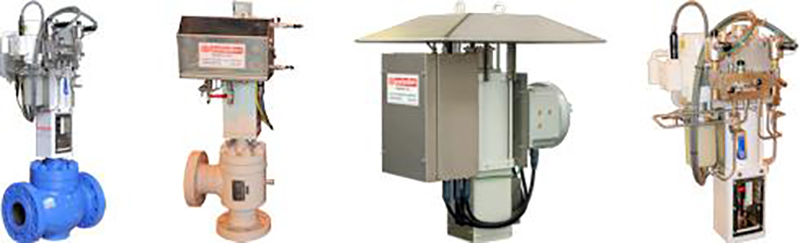
Valve Positioning Systems
Overview
Positional control or proportional valve positioning systems are available using either a pneumatic impulse signal (e.g. 0.2 to 1 Barg) or an electrical signal (normally 4 to 20 mA). These systems are designed either to have customer defined pre-set positions or to have full control of the valve between the open and closed positions. Valve positioning systems can be used in conjunction with on/off production or ESD controls and can be utilised for a partial test system e.g. using digital controllers. PLC controllers can also be incorporated to provide complete automatic valve positioning control via input from pressure transmitters.
Applications
Precise positioning of quarter-turn and linear valves.
Operating Ranges
Electrical Supply (VAC)
380/440V – 3 Phase – 50/60 Cycles
110/240V – Single Phase 50/60 Cycles
Electrical Supply (VDC)
24VDC 50W or 100W
Communications
Command signal: 4-20mA
Re-transmission Signal: 4-20mA
Protocol: 4-20mA HART or Foundation Fieldbus
Accuracy
Positional: Better than ±0.5%
Repeatability: Better than ±0.5%
Temperatures
Low: -60 to +60°C (-76 to +140°F)
Standard: -20 to +60°C (-4 to +140°F)
Key Features & Benefits
The same simplicity and low cost of installation as provided by electric actuators
Fail safe or fail last operation
The power, precision and compact size of high pressure hydraulic systems
Industry-leading control options and system diagnostics
Zero emissions
Environmentally responsible via low power, solar powered and biodegradable fluid options